Brief Overview about Threshing Process
Threshing is the most important procedure taking place all throughout the working mechanism of the combine harvester, once the crops are gathered. It is the separation of the grain from the rest of the crop. This particular task is achieved through the suitable and most appropriate adjustment between the combine concave along with the cylinder. Now the question arises of how to bring upon the most successful threshing grain through the use of the combine harvester. Through a clear understanding about the threshing unit of the combine harvester, the performance of this agricultural equipment can be improved for maximizing the output. The threshing component is undeniably the crux of the combine harvester. Despite of the nature of the machinery farmer utilizes, the main function is to carry out the separation of the kernel from its cob. This is done through friction. This particular action is being obtained through the rotation of the threshing drum against the fixed concave component.
Work Mechanism of Threshing Component of Combine Harvester
• Once the grains are collected, they are subjected to the procedure of threshing. It involves the removal of the threshing grain from the rest of the crops. It is the second procedure of the working mechanism of the combine harvester.
• The threshing component comprises the rotor (rotating cylinder). It has been attached to the moving components. This is including the rasp bars as well as a separating body, concave. The separation of the grain takes place when there occurs the opening of the combine concave.
• Through idle setting and adjustments, the farmer can maximize the material output & optimize the threshing grain separation process.
• The threshing of grains through the combine harvester is capable of preserving the natural shape and at the same time retaining the original quality. It also minimizes the losses of grains taking place during the process of threshing.
Most Common Types of Threshing Units:
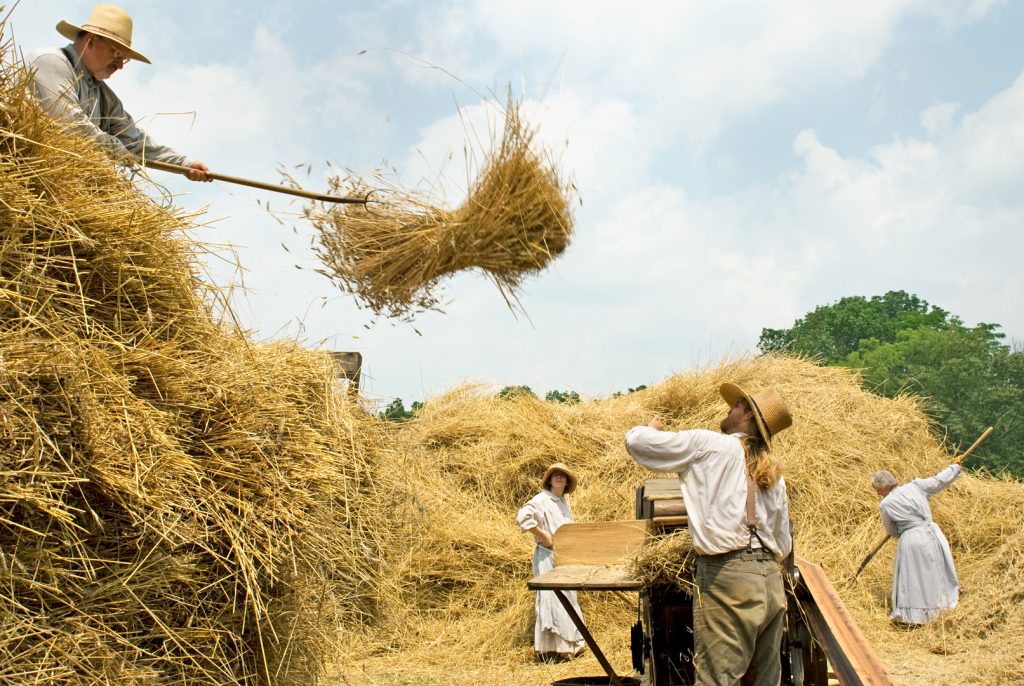
Tangential Threshing Component
This particular part will be including the concave and cylinder. The setting of the clearance between both components is done manually or automatically. The specification of the threshing space is done through the curved region. This particular area is existing between the outer space of the cylinder rotation as well as the inner space of the combine concave.
Axial Threshing Components
This particular unit imbibes the feeding region. Along with that, there are two sections for grain threshing and separating. The cage that relies upon the feeding zone comprises two or even three helical ribs, that have been running into the spaces of grain threshing and separating. This in turn will be creating the helical motion for the material that is subjected to the threshing in this particular region.
Some advantages of the axial unit in comparison to the tangential threshing unit involve:
• Reduced grain damage
• Better grain threshing for all crops
• Improved performance even for wet crop conditions
• Increased work capacity
• Reduced losses
Proper Adjustments of Threshing Unit Is Important For Effective Work
The adjustment aspect of the threshing unit is extremely crucial. It is because of the differences in the types of threshing grains. There are different sizes and textures in the case of both the stem as well as the grains. So, the whole system should be able to carry out the appropriate adjustments for accommodating such differences. To meet the ever-complex as well as diverse needs of farmers, the modern and advanced threshing units of combines are developed for pinpointing specific agriculture requirements.